What Is Lamination in Printing?
- Steve Bates / President @ Citypress
- Apr 30, 2024
- 4 min read
In the printing industry, we use different printing techniques and finishing methods to achieve different effects. One such popular printing finish method is lamination. But what is lamination in printing?
Read on as we explore the lamination process, methods, and types in the printing process.
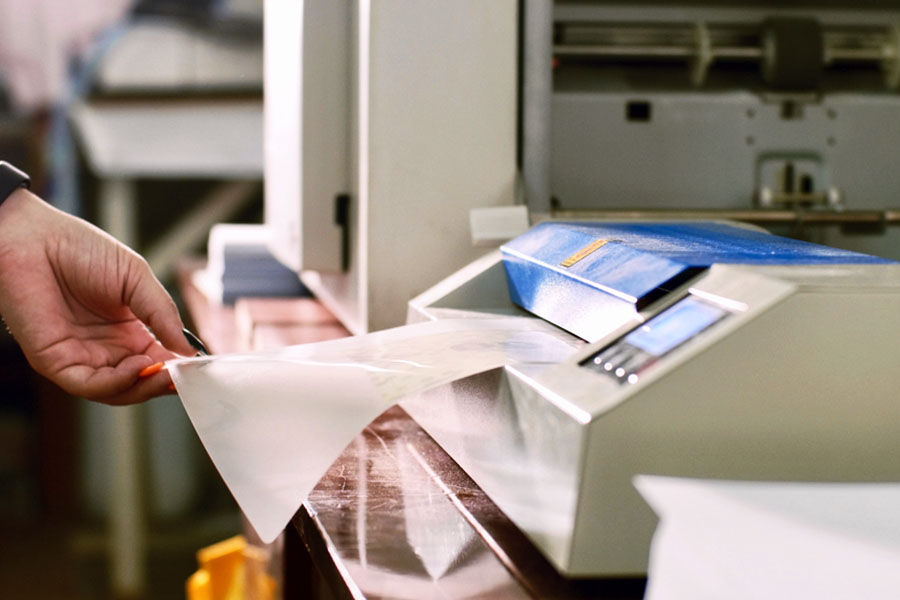
What Is Lamination in Printing?
Lamination is a printing finishing technique that involves using heat and pressure to adhere a thin plastic coating, called a laminate, to paper or card. In other words, lamination is the bonding of plastic film on each side of the print. Many decide to use lamination as a protective layer for the printed material.
Lamination printing is typically used to prolong the life of the item and shield the print from normal wear and tear. The technique of lamination involves covering paper or card sheets with a thin coating of plastic to improve and safeguard printed content.
Gloss, matte, and silk are standard and most often used lamination types. Packaging, book covers, brochures, business cards, and other printed materials are frequently laminated.
With our lamination print finishing solutions, you benefit from increased durability, water resistance, and tear resistance in your prints.
The Lamination Process: How Long Does Paper Lamination Take?
Applying lamination may be applied to a printed product using two printing finish methods: dry bond and wet bond.
For dry bond lamination, we combine two non-porous materials, like film on film or film on foil. During the lamination process, an adhesive (dry bond) is applied to either one or both of the materials. After that, they are dried in an oven, and once dried, we combine the two materials.
In contrast, for wet bond lamination, we also use two materials: a plastic film and a porous substrate (paper or cardstock).
The adhesive (a wet bond) is applied to each material, and the substrates are combined, after which they are dried in an oven. During the time in the oven, the adhesive dries, and both materials adhere to each other.
No matter which method a printer uses, it will take time for the printed paper lamination to dry out. The lamination and drying process may take from 24 to 48 hours.
Types of Lamination in Printing
Your print will feel differently depending on the type of laminated print finish you select, as each offers a very distinct texture. There are many available types of lamination in printing, but the most popular are matte, gloss, and silk.
All of the lamination types will provide you with clear coverage that makes the text and graphics fully visible while increasing the prints' durability.
Your choice of which lamination type to use will depend on what kind of effect you want to achieve and the intended use of the printed product.
Matte lamination
Matte lamination is more suitable if you want to achieve a more natural finish to the printed product. With matt lamination, there is no shine, and it offers a smooth and elegant finish.
Because of the muted effect that matt lamination offers, it may reduce contrast, which gives it a softer look. Matt lamination is an excellent choice if you want to deflect glare and make the print easier to read, be it if exposed to excessive sunlight or even at an angle.
It is also the better choice for prints with subdued color tones. Unlike glossier finishes, matt lamination is softer to the touch, offering a pleasing, velvety feel.

Gloss lamination
Gloss lamination offers a higher level of protection as it can be easily and quickly wiped clean. Gloss lamination is an excellent finish choice for printed products intended to be handled a lot.
The shiny, smooth surface of the glossy lamination makes it more resistant to dirt, smudges, and scratches.
Also, unlike matte lamination, gloss lamination offers a stronger visual impact, making it the better choice for prints with strong, vibrant colors. Besides offering durability and a shiny finish, gloss lamination is also more cost-effective.
Silk lamination
If you are looking for a printing finish that is neither fully matte nor glossy, silk lamination is the right choice. The silk lamination process is similar to traditional lamination with a unique twist.
While it offers strength and durability like traditional lamination, the end result is a soft exterior. With silk lamination, the bold between the paper and the plastic coating is stronger, which leads to a better quality than both matte and silk.
Its name is due to the silk-like appearance it achieves on printed products with a subtle sheen. The unique visual and feel make silk lamination a preferred choice for more upscale products.
Benefits of Lamination in the Printing Industry
Protection
As we have mentioned, protecting your print can be achieved by adding a layer of lamination to your printing. This can help prevent the corners of printed products from wearing out. Lamination makes the printed product last longer without incurring damage like scratches.
Reusable
Laminated printing gives your item additional protection by making it water-resistant. Again, using menus as an example implies that the print on them won't be damaged when you wipe them clean with a cloth or a wipe after each use. The prints will last a long time and can be reused.
Quality
Your print's perceived quality is further enhanced by applying a certain type of printing lamination finish. Glossy lamination printing is a common technique used by magazines to create glossy, eye-catching covers.
This is very helpful for business cards as well, as the texture of the card enhances the first impression of your company. Silk lamination, on the other hand, offers more refined results and is used for upscale products.
Enhanced color
The overall color of your print is also impacted by enhanced color lamination printing. Matt lamination produces a slightly duller color, while gloss lamination intensifies the color.
Colors appear more vibrant when they are laminated with a glossy finish. Whichever effect you want to achieve, there is a type of lamination to choose from.
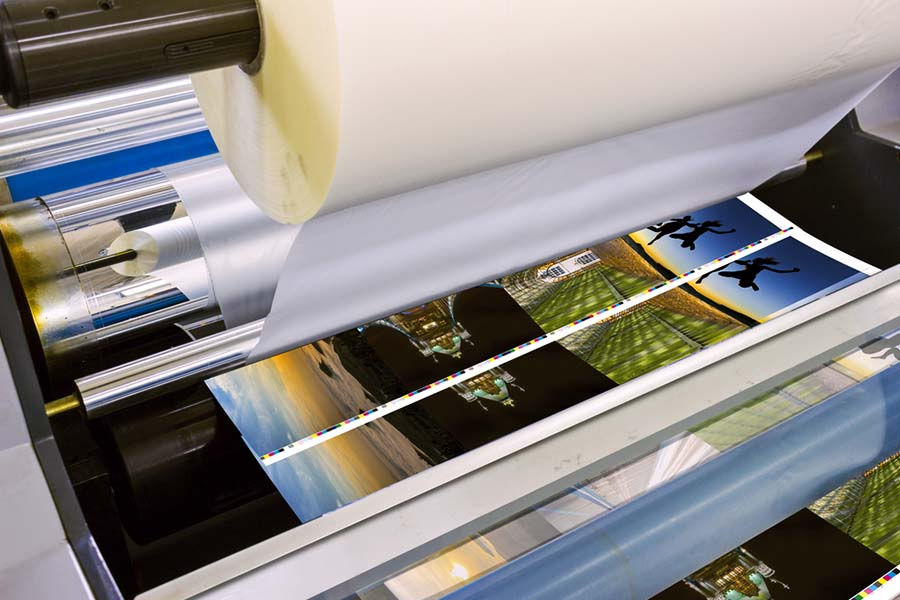
Conclusion
What is lamination in printing? Lamination is the process of bonding plastic coating using heat and pressure to adhere it to a printed product.
The result is a durable surface resistant to scratches, smudges, and dirt, as it is easily cleaned. Depending on the effects you aim to achieve, there are different lamination types, including matte, gloss, and silk.